How does it work?
A biorefinery is a facility that converts biomass into energy and other desirable products through refining, i.e. extracting a product from a raw material. This is done to produce new products based on biomass instead of using fossil raw materials. There are many different uses for a biorefinery, including using biomass from forests, food industry residues or agricultural feedstock. Products that can be produced include aviation fuel, chemicals, textiles, but also electricity, heat and fuel.
In the Green Valleys project, the raw material is grass and clover. We want to use the raw material to produce a high-value protein concentrate that can replace imported soy, which is imported from South America and elsewhere and has a major negative impact on the climate.
The background to the project is Denmark’s intensive cereal cultivation, which leads to major nutrient leakage. The aim was to introduce more grass into the crop rotation to bind nutrients in the soil, while perennial plants also increase carbon storage in the soil and reduce the need for artificial fertilisers and pesticides.
The principle of producing protein concentrate in a biorefinery is to run the grass and clover through a screw press. This produces two fractions: a dry fraction – fibre pulp, and a liquid fraction – green juice. From the green juice, the protein can be separated by heating and centrifuging. The protein then becomes a powder with a protein content of about 50 %, depending on the type of grass used. What remains after the protein has been removed is a liquid called brown juice. The dry fraction, the fibre pulp, can be used as feed for ruminants (fibre pulp) or as a substrate for biogas production. The brown liquor can be used as feed for pigs, for example, or as a substrate for biogas production.
In order to be able to run the plants all year round, the project has tested refining both fresh and ensiled grass and clover. If silage is used, the protein cannot be extracted in the same way because the protein has been broken down in the fermentation process. You then only get a dry fraction and a wet fraction. The wet fraction can be used as feed, for example for pigs, or as a substrate for biogas.
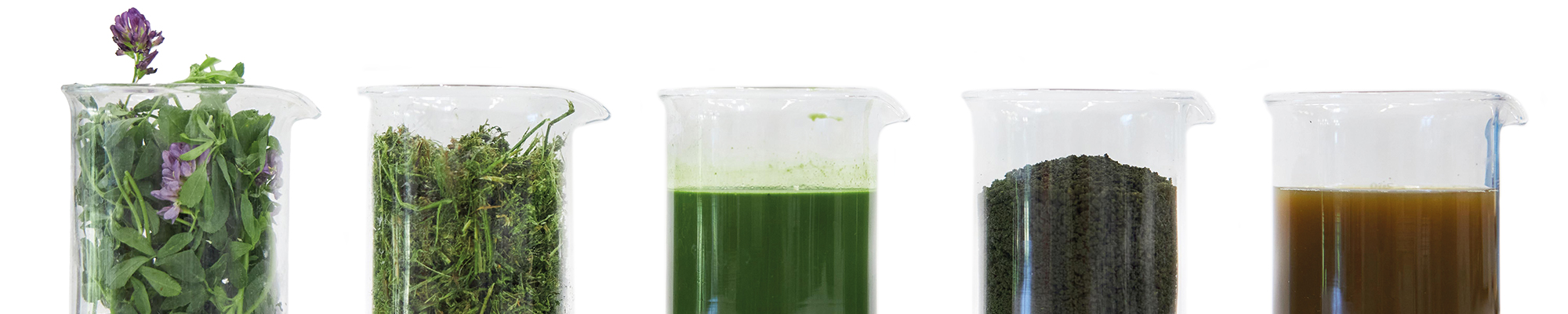
What have we learned from the project Green Valleys
The project Green Valleys has effectively increased the development of green biorefining. The establishment and expansion of two different demonstration and test facilities in Denmark and Sweden respectively has enabled both optimisation on an industrial scale, production of products for testing in feed trials and for trials in bioenergy production. In addition, the establishment has proven to be a highly effective tool to showcase and communicate this new technology to stakeholders in agriculture, industry, and government agencies.
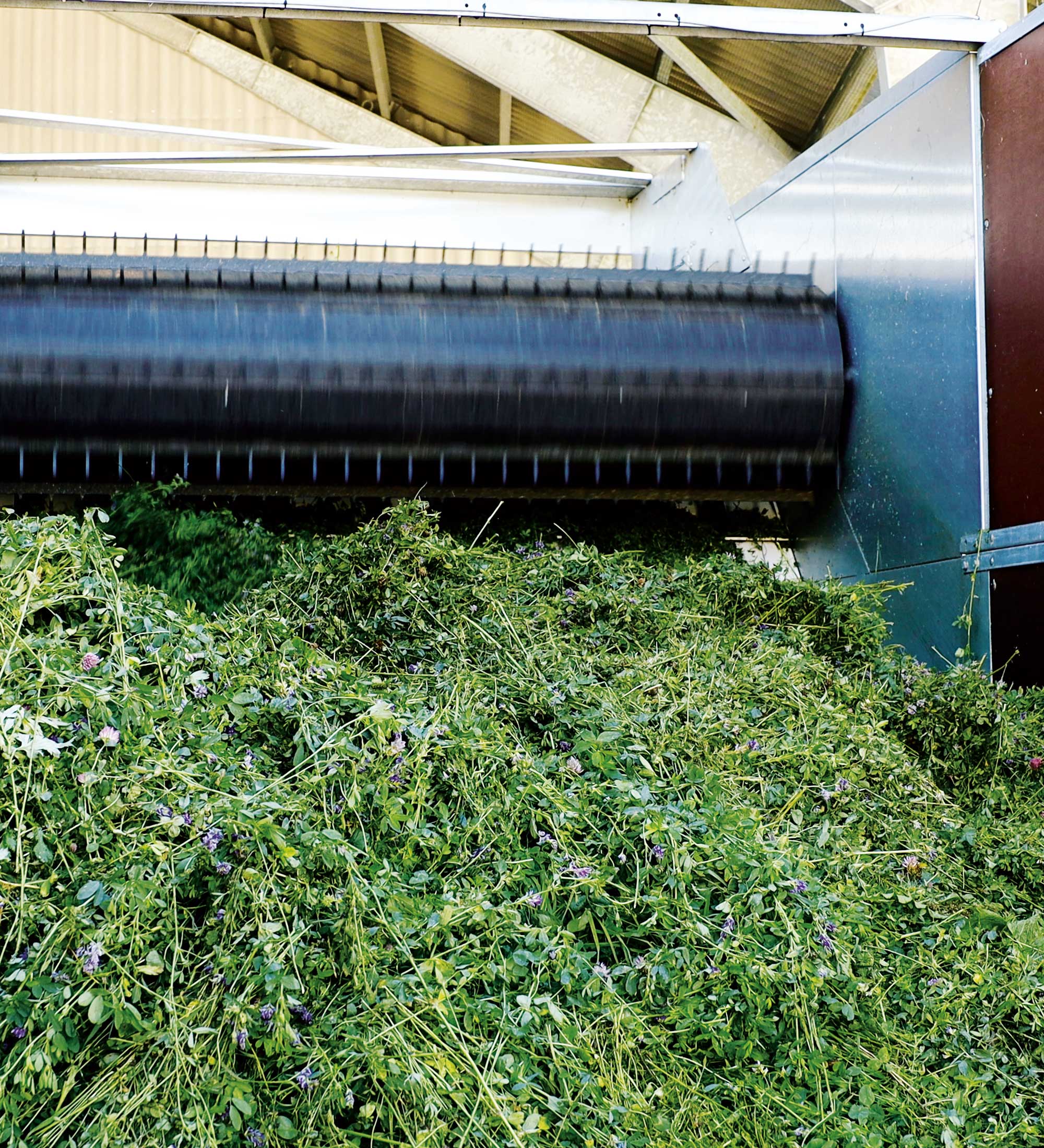
Optimisation of protein concentrates and harvesting methods
During the four years of the Green Valley project, various experiments have been carried out at Aarhus University. These have been carried out at the AU Viborg demonstration farm (Foulum). Experiments have been carried out to optimise the yield of protein concentrate, to optimise the harvesting method to obtain the highest possible yield, and to carry out biogas experiments.
Feeding trials
Within the Green Valleys project, several feeding trials are being conducted to investigate how different grass-based feed solutions affect animal health, growth and production. The trials are a central part of our work to develop more sustainable and resource-efficient feed alternatives for different animal species.
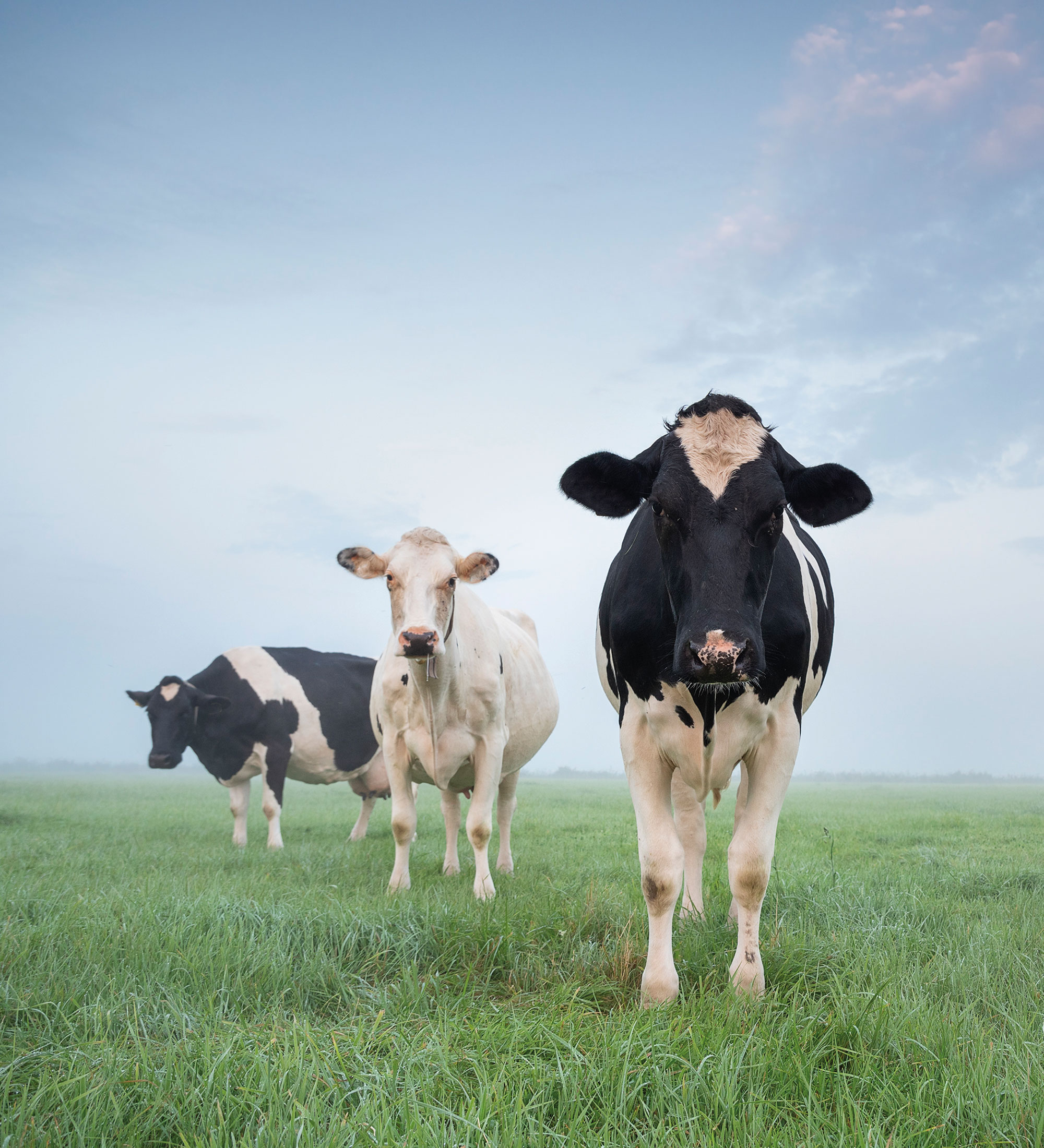
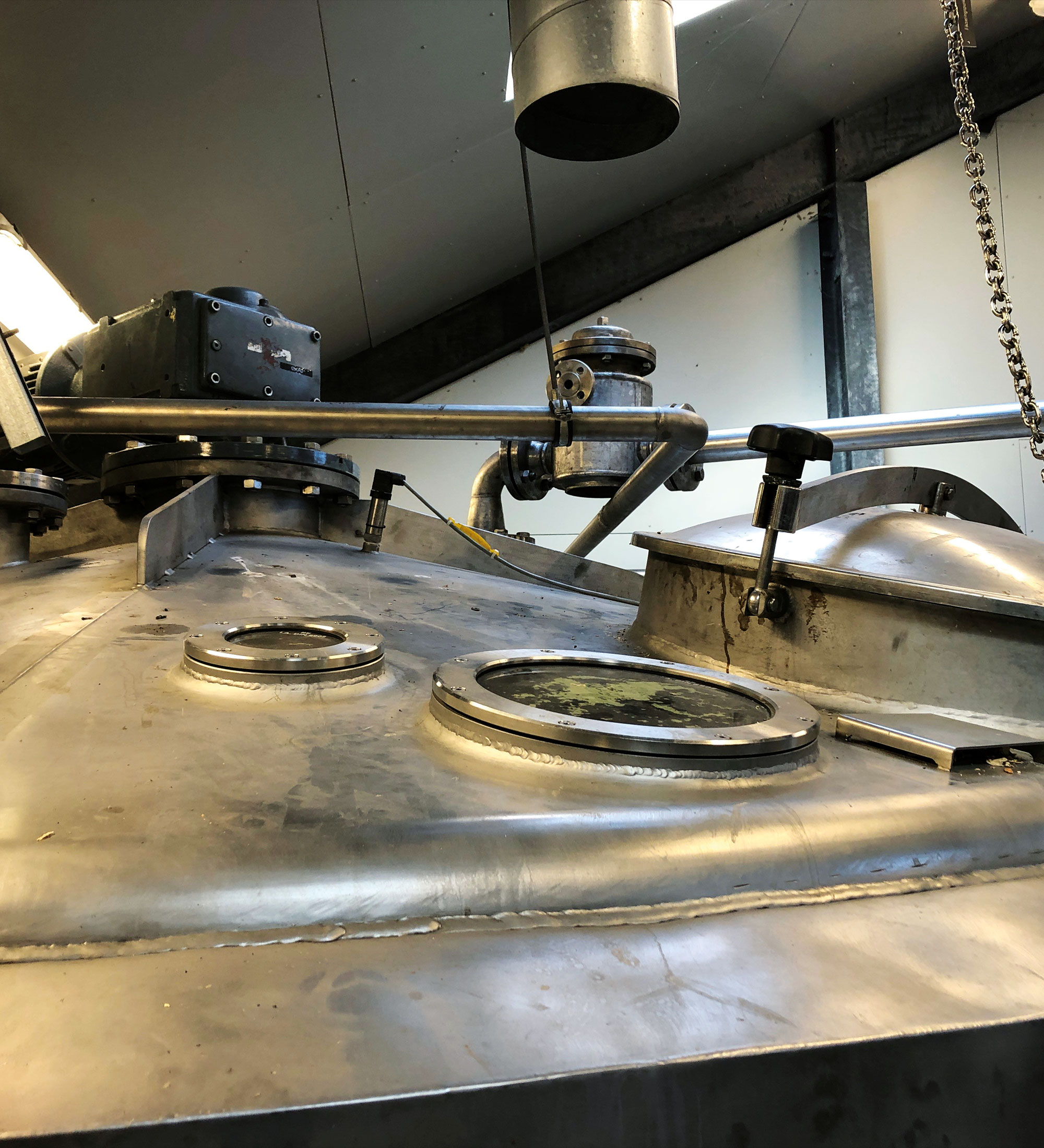
Evaluation of the biomethane potential of the different residual fractions from Sötåsen biorefinery
Hushållningssällskapet Sjuhärad carried out laboratory-scale tests to measure the biomethane potential (BMP) of different mixtures with or without liquid manure from cattle. Green juice and brown juice showed the highest BMP.
Our demonstration platforms
We have two demonstration platforms Sötåsen School of Agriculture and AU Viborg (Research Centre Unit Foulum). Sötåsen is located in Sweden and AU Viborg is located in Denmark.